News
Original reporting, exclusive interviews, and sharp analysis by experienced journalists. Coverage of the breaking and developing news that IT executives need to know about, like moves in the enterprise IT market, major cyberattacks, and more.
Secretary of Homeland Security Alejandro Mayorkas discusses, at the RSA Conference, his department's work and collaborations on cybersecurity.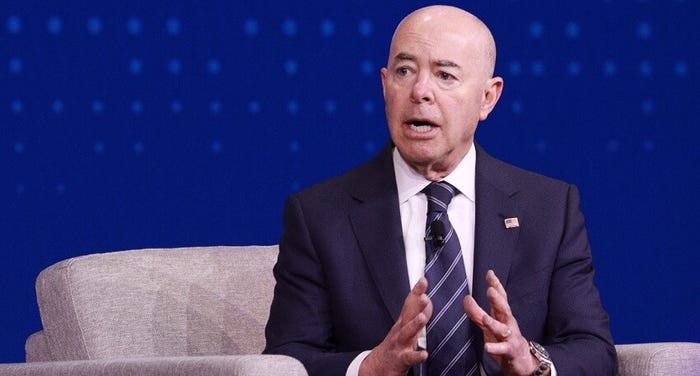
Cyber Resilience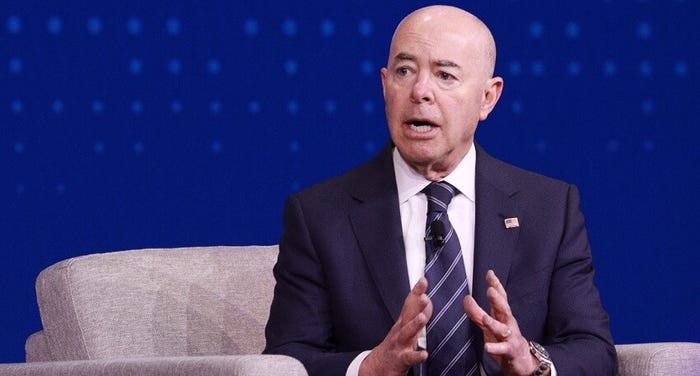
Mayorkas, Easterly at RSAC Talk AI, Security, and Digital DefenseMayorkas, Easterly at RSAC Talk AI, Security, and Digital Defense
Leaders of Homeland Security and CISA hold separate chats to share their stances and campaigns for US cyber resilience, including the Secure by Design campaign.
Never Miss a Beat: Get a snapshot of the issues affecting the IT industry straight to your inbox.